热处理:经过对钢件加热、保温和冷却的操作办法,来改善其内部组织结构,以得到所必须性能的一种加工工艺。
特点:热处理区别于其他加工工艺如铸造、压力加工等的特点是只经过改变工件的组织来改变性能,而不改变其形状。
目的:消除上一工艺产生的材料内部结构缺陷,加强材料性能 ,充分发挥其潜能。
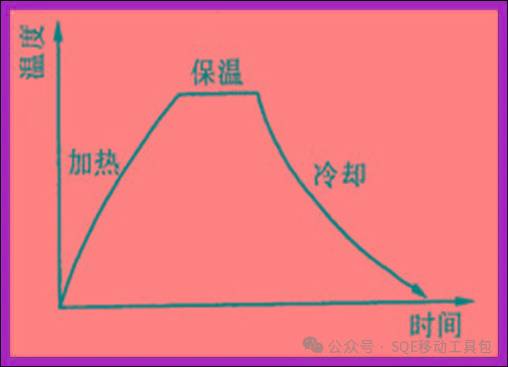
重点包括退火、正火、淬火和回火,是热处理的四种基本工艺,它们在改善金属材料性能、加强制品质量和延长运用寿命等方面发挥着要紧功效。
外加表面热处理工艺,经过改变工件表面的化学成份和组织结构,明显加强了工件的耐磨性、耐蚀性、抗疲劳性和硬度等特性。
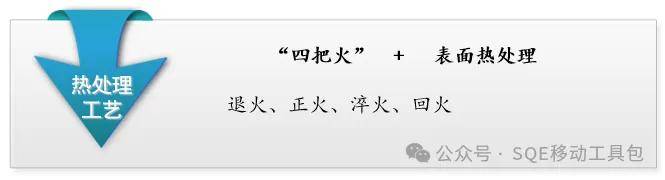
(一)、退火
定义:退火是一种将金属材料加热到适当温度,保持一按时间,而后缓慢冷却的热处理工艺。退火的重点目的是降低材料的硬度,加强塑性,以利于切削加工或压力加工;细化晶粒,改善组织以加强材料的力学性能;消除残余应力,稳定尺寸,减少变形与裂纹倾向。按照加热温度的不同,退火可分为完全退火、球化退火、去应力退火等。
组织:铁素体、层状珠光体、球状珠光体、颗粒状渗碳体
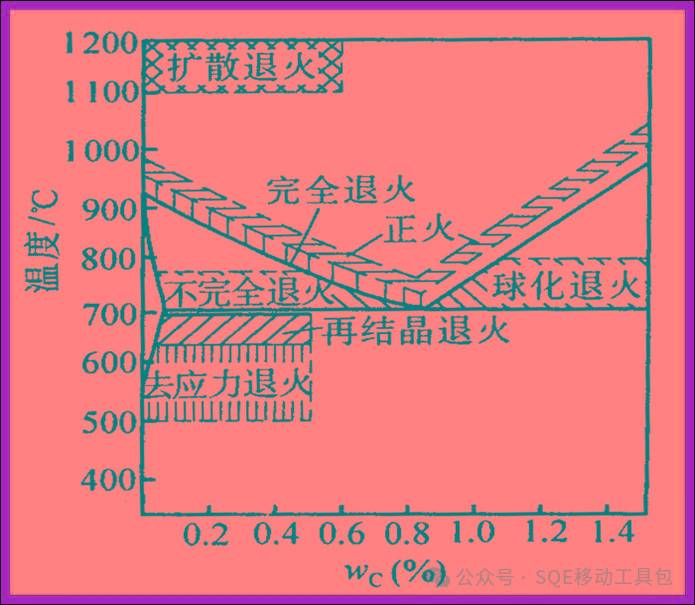
(二)、正火
定义:正火是将金属材料加热到Ac3或Acm以上30~50℃,保温后在空气中冷却的热处理办法。正火的重点目的是细化组织,改善钢的性能,得到接近平衡状态的组织。与退火相比,正火拥有操作简便、生产周期短、成本低和能耗少等优点,因此呢在实质生产中应用较多。另外,正火还可做为低碳钢及低合金钢铸件、锻件及焊件的最后热处理,或做为某些工件的预先热处理。
组织:铁素体和索氏体
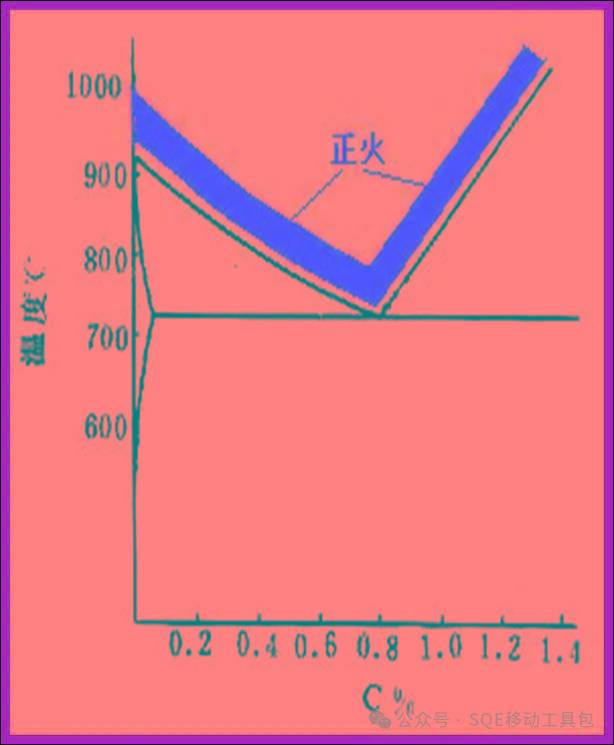
(三)、淬火
定义:淬火是将金属材料加热到奥氏体区域温度,保持一按时间后,快速冷却的热处理办法。淬火的重点目的是使金属材料得到马氏体组织,从而加强材料的硬度、强度和耐磨性。淬火后的金属材料一般拥有较高的硬度和脆性,因此呢必须进行回火处理以调节其性能。
组织:马氏体,残余奥氏体,颗粒状渗碳体
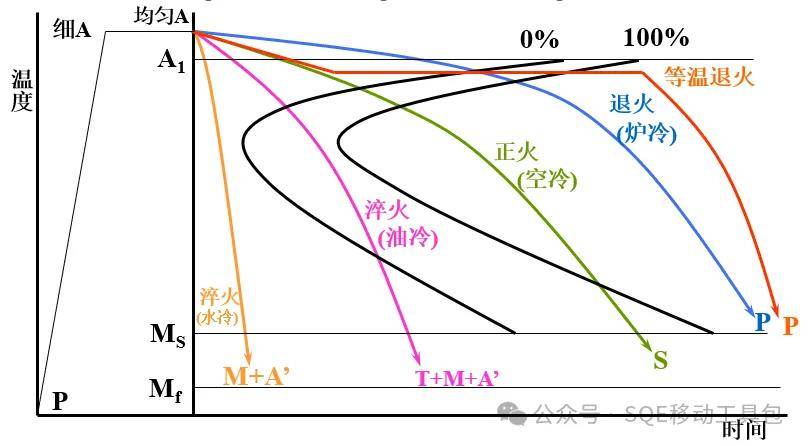
(四)、回火
定义:回火是将淬火后的金属材料加热到小于下临界温度A1的适当温度,保持一按时间后,再冷却到室温的热处理办法。回火的重点目的是降低材料的脆性,消除或减少内应力,加强塑性和韧性,使材料在运用过程中很难出现脆性断裂。另外,回火还能够调节材料的力学性能和硬度,以满足不同的运用需求。
预处理:淬火;淬火钢在回火过程中,回火温度—回火组织—钢的性能之间存在着一一对应关系。
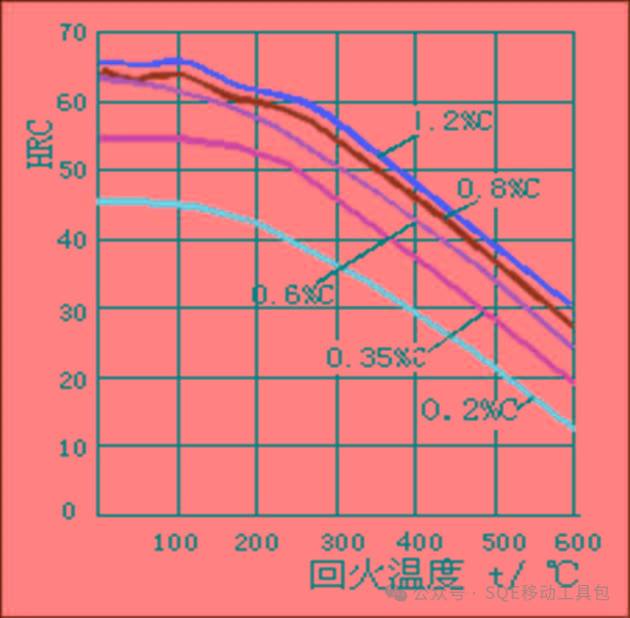
1)低温回火:
温度范围:一般在150~250℃之间。
组织变化:工件中重点形成回火马氏体,这种组织在显微镜下呈暗黑色片状,比淬火马氏体更易受腐蚀。
目的与用途:重点目的是保持淬火工件的高硬度和耐磨性,同期降低淬火残留应力和脆性。因此呢,低温回火后的材料一般用于制作量具、刀具和滚动轴承等需求高硬度和耐磨性的零件。
2)中温回火:
温度范围:一般在350~500℃之间。
组织变化:工件中重点形成回火屈氏体,其特点是α相仍保持板条状或片状形态,上面分布着微细粒状渗碳体。
目的与用途:中温回火的重点目的是得到良好的弹性和韧性,以及必定的硬度。因此呢,中温回火后的材料一般用于制作弹簧、锻模等必须良好弹性和韧性的零件。
3)高温回火:
温度范围:一般在500~650℃之间。
组织变化:工件中重点形成回火索氏体,这种组织由细粒状渗碳体和等轴状铁素体形成。
目的与用途:高温回火的重点目的是得到良好的综合力学性能,如高强度、弹性极限和较高的韧性。因此呢,高温回火后的材料广泛用于各样较要紧的受力结构件,如连杆、螺栓、齿轮及轴类零件等。另外,淬火后的工件经高温回火后,其组织稳定,尺寸变化小,因此呢亦常常做为精细零件或感应淬火件的预先热处理。
(五)、表面热处理
表面热处理工艺是热处理技术中的要紧分支,重点目的是经过改变工件表面的化学成份、组织结构和性能,以加强其耐磨性、耐蚀性、抗疲劳性和硬度等特性。其中,表面淬火、化学渗碳和渗氮是三种平常的表面热处理工艺。
1. 表面淬火
工艺原理:表面淬火是经过快速加热工件表面至淬火温度,而后快速冷却,使表面层得到马氏体或贝氏体组织,而心部仍保持原组织的一种热处理工艺。
目的与用途:表面淬火的重点目的是加强工件表面的硬度和耐磨性,同期保持心部良好的韧性和强度。这种工艺常用于中碳钢和低合金钢制造的零件,如齿轮、轴、曲轴等。
工艺办法:感应加热、火焰加热
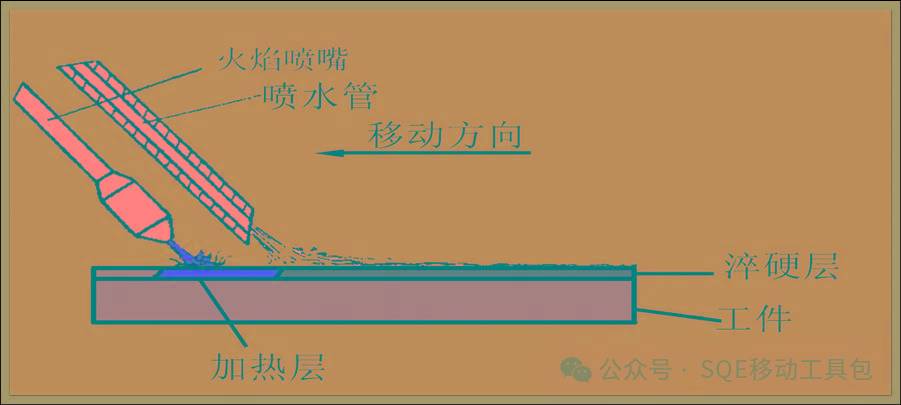
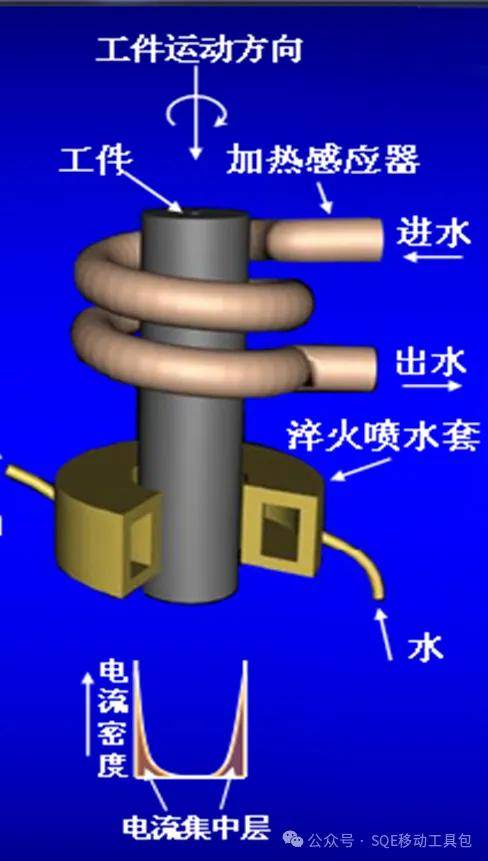
2. 化学热处理
定义:将工件置于特定的介质中加热、保温,使介质中的活性原子渗入工件表层,以改变表层的化学成份、组织和性能的一种热处理工艺。
基本机理:渗剂分解出活性原子-》工件表面吸收活性原子-》活性原子从工件表层向内部的扩散
具备前提:(1)工件有吸收这些元素的能力。(2)渗入元素应具备活性
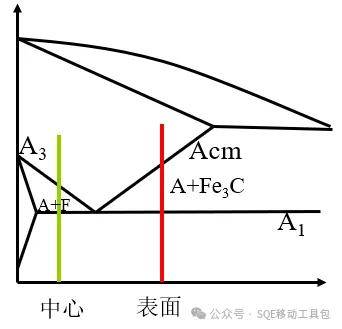
1)表面渗碳
工艺原理:化学渗碳是将工件置于含碳介质中,加热至必定温度,使碳原子渗入工件表面,从而增多工件表面碳含量的过程。渗碳后的工件一般必须再进行淬火和回火处理,以得到所需的表面硬度和心部韧性。
目的与用途:化学渗碳的重点目的是加强工件表面的碳含量和硬度,以增多耐磨性和疲劳强度。这种工艺常用于制造承受重载和冲击的零件,如汽车或机床的齿轮、轴等。
特点:渗碳后的工件表面硬度达到HRC58-65,心部硬度较低,拥有良好的抗疲劳性能。另外,渗碳处理还能够加强工件的抗腐蚀性。
渗碳工艺:加热温度为900~950℃;渗碳时间通常为3~9小时;
渗碳后组织:表面的含碳量最高:wc=1.0%上下,由表及里,含碳量逐步降低,直至原始含碳量。
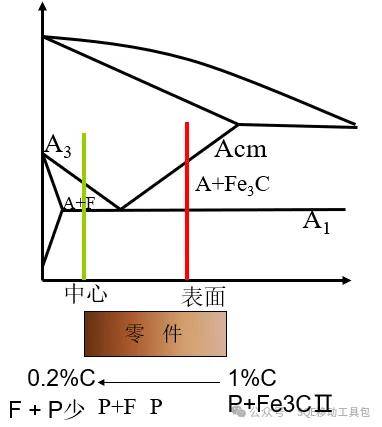
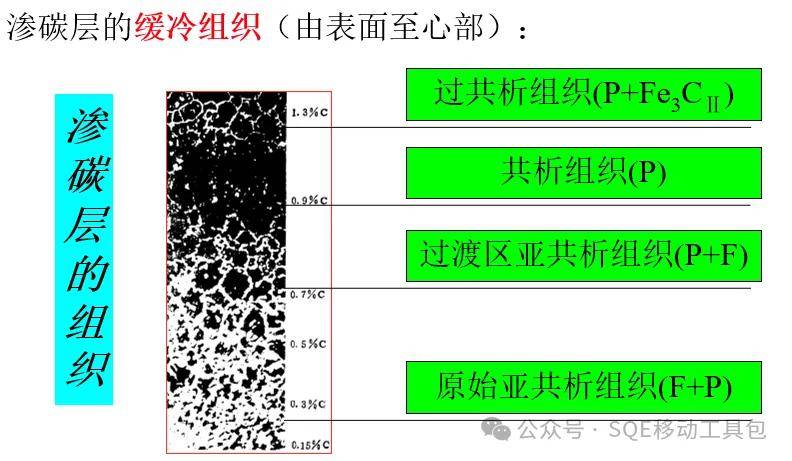
2)表面渗氮
工艺原理:渗氮是将工件置于含氮介质中,加热至必定温度,使氮原子渗入工件表面,形成氮化层的过程。渗氮过程中,氮与工件表面的铁原子出现化学反应,生成氮化铁等化合物。
目的与用途:渗氮的重点目的是加强工件表面的硬度、耐磨性和耐蚀性。渗氮处理常用于制造精细零件、模具和高速切削工具等。
缺点:渗氮时间长,通常长于30小时。渗层薄,通常为几十至几百微米。
特点(与渗碳比较):
1.更高的硬度,更高的耐磨性,HV950~1200。如38CrMoAl,渗C淬火,HRC58~63;渗N后,相当于HRC65~72;
2.拥有高的红硬性。渗C工件只适用于在<200℃工作,而渗N可在500~600℃工作;
3.拥有高残余压应力。表层形成比容更大的高氮相ε(Fe3N);
4.工件变形小。由于渗氮温度低,且随后不需淬火;
5.有良好的抗蚀性。这是因为有致密、稳定的ε相,然则渗氮层中的ε相(N:8.25~11%),脆性很强;渗层较薄,承载能力不及渗C淬火。
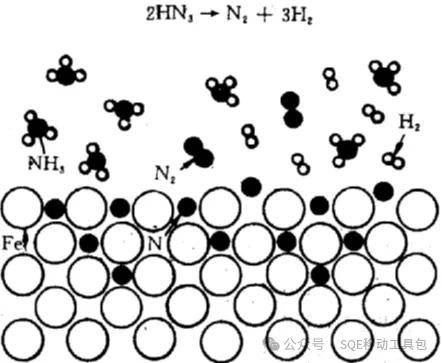
以上介绍了热处理的四把火和表面处理的关联知识,在实质生产过程中,必须按照材料的成份、组织和性能需求,恰当选取热处理办法和工艺参数,以得到最佳的综合性能。
[声明]本文源自网络,由轧机轴承整理颁布,版权归原作者所有。转载请注明源自,如有侵权,请联系咱们删除。
更加多精彩内容,都在【轧机轴承】公众号。返回首页,查看更加多
外链论坛:http://www.fok120.com/
|